|
The Preservation and Repair of Historic Stucco
By Anne Grimmer
Stucco is a material of deceptive simplicity: in most cases its repair should not be undertaken by a property owner unfamiliar with the art of plastering. Successful stucco repair requires the skill and experience of a professional plasterer.
Some of the earliest stucco buildings in the United States include examples of the Federal, Greek and Gothic Revival styles of the eighteenth and the nineteenth centuries that emulated European architectural fashions.
The introduction of the many revival styles of architecture around the turn of the twentieth century, combined with the improvement and increased availability of portland cement resulted in a "craze" for stucco as a building material in the United States. Beginning about 1890 and gaining momentum into the 1930s and 1940s, stucco was associated with certain historic architectural styles, including: Prairie; Art Deco, and Art Moderne; Spanish Colonial, Mission, Pueblo, Mediterranean, English Cotswold Cottage, and Tudor Revival styles; as well as the ubiquitous bungalow and "four-square" house. The fad for Spanish Colonial Revival, and other variations on this theme, was especially important in furthering stucco as a building material in the United States during this period, since stucco clearly looked like adobe.
The appearance of much stucco was determined by the color of the sand--or sometimes burnt clay--used in the mix, but often stucco was also tinted with natural pigments, or the surface whitewashed or color-washed after stuccoing was completed. Brick dust could provide color, and other coloring materials that were not affected by lime, mostly mineral pigments, could be added to the mix for the final finish coat. Stucco was also marbled or marbleized--stained to look like stone by diluting oil of vitriol (sulfuric acid) with water, and mixing this with a yellow ochre, or another color. As the twentieth century progressed, manufactured or synthetic pigments were added at the factory to some prepared stucco mixes.
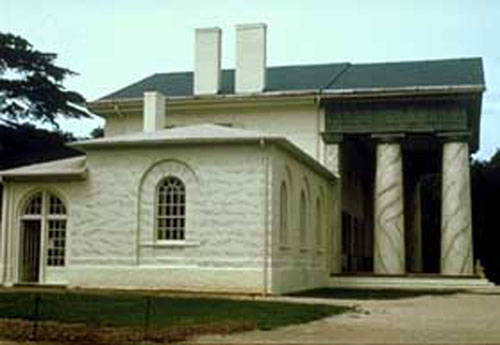
The stucco finish on Arlington House, Arlington, Virginia, was marbleized in the 1850s, approximately 30 years after it was built. Photo: NPS files.
Stucco is applied directly, without lath, to masonry substrates such as brick, stone, concrete or hollow tile. But on wood structures, stucco, like its interior counterpart plaster, must be applied over lath in order to obtain an adequate key to hold the stucco.
Like interior wall plaster, stucco has traditionally been applied as a multiple-layer process, sometimes consisting of two coats, but more commonly as three. Whether applied directly to a masonry substrate or onto wood or metal lath, this consists of a first "scratch" or "pricking-up" coat, followed by a second scratch coat, sometimes referred to as a "floating" or "brown" coat, followed finally by the "finishing" coat.
Until the early-twentieth century when a variety of novelty finishes or textures were introduced, the last coat of stucco was commonly given a smooth, troweled finish, and then scored or lined in imitation of ashlar. The illusion of masonry joints was sometimes enhanced by a thin line of white lime putty, graphite, or some other pigment. Some nineteenth century buildings feature a water table or raised foundation of roughcast stucco that differentiates it from the stucco surface above, which is smooth and scored. Other novelty or textured finishes associated with the "period" or revival styles of the early-twentieth century include: the English cottage finish, adobe and Spanish, pebble-dashed or dry-dash surface, fan and sponge texture, reticulated and vermiculated, roughcast (or wet dash), and sgraffito.
Although A. J. Downing alluded to stuccoed houses in Pennsylvania that had survived for over a century in relatively good condition, historic stucco is inherently not a particularly permanent or long-lasting building material. Regular maintenance is required to keep it in good condition. Unfortunately, many older or historic buildings are not always accorded this kind of care.
After the cause of deterioration has been identified, any necessary repairs to the building should be made first before repairing the stucco. Such work is likely to include repairs designed to keep excessive water away from the stucco, such as roof, gutter, downspout and flashing repairs, improving drainage, and redirecting rainwater runoff and splash-back away from the building.
Previous repairs inexpertly carried out may have caused additional deterioration, particularly if executed in portland cement, which tends to be very rigid, and therefore incompatible with early, mostly soft lime-based stucco that is more "flexible." Incompatible repairs, external vibration caused by traffic or construction, or building settlement can also result in cracks which permit the entrance of water and cause the stucco to fail.
Before beginning any stucco repair, an assessment of the stucco should be undertaken to determine the extent of the damage, and how much must be replaced or repaired.
Analysis of the historic stucco will provide useful information on its primary ingredients and their proportions, and will help to ensure that the new replacement stucco will duplicate the old in strength, composition, color and texture as closely as possible.
In the interest of saving or preserving as much as possible of the historic stucco, patching rather than wholesale replacement is preferable. When repairing heavily textured surfaces, it is not usually necessary to replace an entire wall section, as the textured finish, if well-executed, tends to conceal patches, and helps them to blend in with the existing stucco. However, because of the nature of smooth-finished stucco, patching a number of small areas scattered over one elevation may not be a successful repair approach unless the stucco has been previously painted, or is to be painted following the repair work. On unpainted stucco such patches are hard to conceal, because they may not match exactly or blend in with the rest of the historic stucco surface. For this reason it is recommended, if possible, that stucco repair be carried out in a contained or well-defined area, or if the stucco is scored, the repair patch should be "squared-off" in such a way as to follow existing scoring. In some cases, especially in a highly visible location, it may be preferable to restucco an entire wall section or feature. In this way, any differences between the patched area and the historic surface will not be so readily apparent.
Choosing a stucco mix that is durable and compatible with the historic stucco on the building is likely to involve considerable trial and error, and probably will require a number of test samples, and even more if it is necessary to match the color. It is best to let the stucco test samples weather as long as possible--ideally one year, or at least through a change of seasons, in order to study the durability of the mix and its compatibility with the existing stucco, as well as the weathering of the tint if the building will not be painted and color match is an important factor.
If the test samples are not executed on the building, they should be placed next to the stucco remaining on the building to compare the color, texture and composition of the samples with the original. The number and thickness of stucco coats used in the repair should also match the original. The finish coat should be worked to match the texture of the original stucco.
The color of most early stucco was supplied by the aggregate included in the mix--usually the sand. Sometimes natural pigments were added to the mix, and eighteenth and nineteenth-century scored stucco was often marbleized or painted in imitation of marble or granite. Stucco was also frequently coated with whitewash or a colorwash. This tradition later evolved into the use of paint, its popularity depending on the vagaries of fashion as much as a means of concealing repairs. Because most of the early colors were derived from nature, the resultant stucco tints tended to be mostly earth-toned. This was true until the advent of brightly colored stucco in the early decades of the twentieth century. This was the so-called "Jazz Plaster" developed by O.A. Malone, the "man who put color into California," and who founded the California Stone Products Corporation in 1927. California Stucco was revolutionary for its time as the first stucco/plaster to contain colored pigment in its pre-packaged factory mix.
When patching or repairing a historic stucco surface known to have been tinted, it may be possible to determine through visual or microscopic analysis whether the source of the coloring is sand, cement, or pigment. Although some pigments or aggregates used traditionally may no longer be available, a sufficiently close color-match can generally be approximately using sand, natural or mineral pigments, or a combination of these.
Many stucco buildings have been painted over the years and will require repainting after the stucco repairs have been made. Limewash or cement-based paint, latex paint, or oil-based paint are appropriate coatings for stucco buildings. The most important factor to consider when repainting a previously painted or coated surface is that the new paint be compatible with any coating already on the surface.
If the structure must be painted for the first time to conceal repairs, almost any of these coatings may be acceptable depending on the situation. Latex paint, for example, may be applied to slightly damp walls or where there is an excess of moisture, but latex paint will not stick to chalky or powdery areas. Oil-based, or alkyd paints must be applied only to dry walls; new stucco must cure up to a year before it can be painted with oil-based paint.
There are many contemporary stucco products on the market today. Many of them are not compatible, either physically or visually, with historic stucco buildings. Such products should be considered for use only after consulting with a historic masonry specialist. However, some of these prepackaged tinted stucco coatings may be suitable for use on stucco buildings dating from the late-nineteenth or early-twentieth century, as long as the color and texture are appropriate for the period and style of the building. While some masonry contractors may, as a matter of course, suggest that a water-repellent coating be applied after repairing old stucco, in most cases this should not be necessary, since color washes and paints serve the same purpose, and stucco itself is a protective coating.
Complete replacement of the historic stucco with new stucco of either a traditional or modern mix will probably be necessary only in cases of extreme deterioration-- that is, a loss of bond on over 40-50 percent of the stucco surface. Another reason for total removal might be that the physical and visual integrity of the historic stucco has been so compromised by prior incompatible and ill-conceived repairs that patching would not be successful.
Most of the oldest stucco in the U.S. dating prior to the late-nineteenth century, will generally have a smooth, troweled finish (sometimes called a sand or float finish), possibly scored to resemble ashlar masonry units. Scoring may be incised to simulate masonry joints, the scored lines may be emphasized by black or white penciling, or the lines may simply be drawn or painted on the surface of the stucco. In some regions, at least as early as the first decades of the nineteenth century, it was not uncommon to use a roughcast finish on the foundation or base of an otherwise smooth-surfaced building. Roughcast was also used as an overall stucco finish for some outbuildings, and other less important types of structures.
A wide variety of decorative surface textures may be found on revival style stucco buildings, particularly residential architecture. These styles evolved in the late-nineteenth century and peaked in popularity in the early decades of the twentieth century. Frank Lloyd Wright favored a smooth finish stucco, which was imitated on much of the Prairie style architecture inspired by his work. Some of the more picturesque surface textures include: English Cottage or English Cotswold finish; sponge finish; fan texture; adobe finish; and Spanish or Italian finish. Many of these finishes and countless other regional and personalized variations on them are still in use.
The most common early-twentieth century stucco finishes are often found on bungalow-style houses, and include: spatter or spatterdash (sometimes called roughcast, harling, or wetdash), and pebble-dash or drydash. The spatterdash finish is applied by throwing the stucco mortar against the wall using a whisk broom or a stiff fiber brush, and it requires considerable skill on the part of the plasterer to achieve a consistently rough wall surface. The mortar used to obtain this texture is usually composed simply of a regular sand, lime, and cement mortar, although it may sometimes contain small pebbles or crushed stone aggregate, which replaces one-half the normal sand content. The pebble-dash or drydash finish is accomplished manually by the plasterer throwing or "dashing" dry pebbles (about 1/8" to 1/4" in size), onto a coat of stucco freshly applied by another plasterer. The pebbles must be thrown at the wall with a scoop with sufficient force and skill that they will stick to the stuccoed wall. A more even or uniform surface can be achieved by patting the stones down with a wooden float. This finish may also be created using a texturing machine.
Historic stucco is a character-defining feature and should be considered an important historic building material, significant in its own right. When repairing historic stucco, the new stucco should duplicate the old as closely as possible in strength, composition, color and texture.
Selected Reading
Grimmer, Anne E. Keeping it Clean: Removing Exterior Dirt, Paint, Stains and Graffiti from Historic Masonry Buildings.
Washington, D.C.: National Park Service, U.S. Department of the Interior, 1988.
Hodgson, Frederick T. Plaster and Plastering, Mortars and Cements, How to Make, and How to Use with An Illustrated Glossary of Terms.
New York: The Industrial Publication Company, 1901.
Jowers, Walter. "Bungalow Building Materials: How to Repair Stucco." The Old-House Journal. Vol. XIII, No. 4 (May 1985), pp. 8083.
MacDonald, Marylee. Preservation Briefs 21: Repairing Historic Flat Plaster-Walls and Ceilings.
Washington, D.C.: National Park Service, U.S. Department of the Interior, 1989.
Editors note: Reprinted from Preservation Briefs #22, Technical Preservation Services, National Park Service, US Department of the Interior, and heavily edited. To view in its entirety please go to: www.cr.nps.gov/hps/tps/briefs/brief22.htm |
MORE FROM THIS ISSUE
Root of the Problem?
Is it Worth Saving?
Making History
New Project to Reconfigure Tank Farm
Coronado City Council Upholds Designation by the City's Historical Resources Commission
Historic Preservation: The Greenest of Conservation Solutions
Adobe U
The Preservation and Repair of Historic Stucco
Borrego Springs Modern
Modern for the Masses
Community Outreach
Old Town Cultural/Historical Program
Annual Report
Statement of Activities
Statement of Financial Position
Head Docent Promoted
In Memoriam: Lee Roper (1929-2006)
Squire Ensworth's Letters to Mr. Whaley
Whaley House Garden
Volunteer Profile: Pat Petersen
SOHO Highlights San Diego County Museums
1938 Midway La Playa Trail Refurbished & Unveiled
What is it?
Strength in Numbers
Lost San Diego
DOWNLOAD full magazine as pdf (8.9mb)
|